Heat Exchanger Process Data Sheet Downloads: Key Considerations and Challenges
A heat exchanger process data sheet is a crucial document in the selection, design, and operation of heat exchangers in industrial applications. These data sheets provide essential process parameters, design specifications, and operational conditions necessary for engineers and manufacturers to develop efficient heat exchange systems. The availability of standardized and well-structured heat exchanger process data sheet downloads simplifies decision-making, enhances system performance, and ensures compliance with industry standards.
PROCESS DATA SHEETHEAT EXCHANGERSTATIC EQUIPMENTS
Introduction of Heat Exchanger Process Data Sheet
A heat exchanger process data sheet is a crucial document in the selection, design, and operation of heat exchangers in industrial applications. These data sheets provide essential process parameters, design specifications, and operational conditions necessary for engineers and manufacturers to develop efficient heat exchange systems. The availability of standardized and well-structured heat exchanger process data sheet downloads simplifies decision-making, enhances system performance, and ensures compliance with industry standards.
This article explores the importance of process data sheets, key factors influencing their preparation and use, and the trade-offs associated with different approaches. Additionally, it highlights challenges and best practices in leveraging process data sheets for optimal heat exchanger performance.
Understanding the Heat Exchanger Process Data Sheet
A process data sheet for a heat exchanger serves as a bridge between process engineers and equipment designers. It contains essential details that dictate the efficiency, size, material selection, and thermal performance of the heat exchanger.
Key Components of a Heat Exchanger Process Data Sheet:
Process Information: Includes details such as fluid properties, flow rates, inlet and outlet temperatures, pressure conditions, and thermal duties.
Heat Transfer Characteristics: Specifies required heat load, heat transfer coefficients, and temperature differences.
Mechanical Design Parameters: Covers material selection, corrosion allowance, pressure drop limitations, and construction codes.
Operational and Maintenance Considerations: Provides guidelines for cleaning, inspection, and expected operational life.
Regulatory and Safety Compliance: Lists standards like ASME, TEMA, API, and PED, which the heat exchanger must adhere to.
Key Factors Impacting Heat Exchanger Process Data Sheets
When downloading or preparing a heat exchanger process data sheet, several crucial factors must be considered:
1. Fluid Properties and Flow Rates
The type of fluids used (gas, liquid, steam) significantly affects heat transfer rates.
Viscosity, specific heat, and thermal conductivity impact exchanger efficiency.
Imbalance in flow rates between the hot and cold sides can lead to inefficiencies and potential fouling issues.
2. Temperature and Pressure Conditions
The difference in inlet and outlet temperatures dictates heat exchanger size.
Higher pressures require robust construction materials, impacting costs and longevity.
Pressure drops must be optimized to avoid excessive energy consumption in pumps or fans.
3. Material Selection
Materials must be chosen based on corrosion resistance, temperature tolerance, and cost.
Stainless steel, titanium, and exotic alloys are preferred for aggressive fluids.
Improper material selection can lead to early failure and increased maintenance costs.
4. Heat Load and Performance Requirements
The required heat duty (measured in kW or BTU/hr) determines exchanger size and design.
Balancing heat duty with space and budget constraints is a major design challenge.
5. Regulatory Compliance and Safety Standards
Compliance with ASME, TEMA, or API ensures safety and reliability.
Non-compliance may result in operational risks, increased liabilities, and regulatory penalties.
Trade-Offs in Designing and Selecting Heat Exchangers
Every decision in the heat exchanger process data sheet preparation involves trade-offs:
Performance vs. Cost
High-efficiency designs (e.g., plate heat exchangers) are costlier but reduce energy usage.
Lower-cost options (e.g., shell and tube) may have higher operational expenses.
Material Strength vs. Weight
Heavy-duty materials improve longevity but increase installation and transportation costs.
Lightweight materials reduce weight but may require frequent replacements.
Compactness vs. Maintainability
Smaller exchangers save space but are harder to clean and maintain.
Larger units facilitate cleaning but require more floor space.
Pressure Drop vs. Heat Transfer Efficiency
Increasing surface area improves heat transfer but can cause excessive pressure drops, increasing pump energy costs.
Challenges in Heat Exchanger Process Data Sheet Downloads
1. Data Accuracy and Consistency
Inaccurate process data leads to inefficient exchanger design and operational failures.
Data sheets from different sources may have conflicting formats and parameters.
2. Compatibility with Software and Design Tools
Engineers often need data in specific formats (Excel, PDF, or simulation software-compatible files).
Lack of integration with design tools can slow down the project timeline.
3. Understanding and Interpretation by Engineers
Complex technical terminology in data sheets can lead to misinterpretation.
Standardization efforts like TEMA classifications help mitigate this issue.
4. Customization and Updates
Many downloaded process data sheets may not cater to site-specific requirements.
Real-time updates are necessary to account for process changes and operational modifications.
Best Practices for Utilizing Heat Exchanger Process Data Sheets
To maximize the benefits of heat exchanger process data sheet downloads, follow these best practices:
Standardize Data Sheet Formats
Use industry-standard templates (ASME, TEMA) to ensure clarity and consistency.
Maintain structured formats that facilitate quick decision-making.
Ensure Data Accuracy Before Design
Verify all input parameters before using them in selection software.
Cross-check with multiple sources to avoid costly design errors.
Use Advanced Selection and Simulation Tools
Employ software like HTRI, Aspen Exchanger Design, or HEXTRAN to validate data sheets.
Ensure compatibility with the plant's operational environment.
Incorporate Lifecycle Cost Analysis
Consider long-term operational and maintenance costs rather than just initial costs.
Account for energy savings, downtime reduction, and material longevity.
Regularly Update Data Sheets
Keep documentation updated based on real-time performance monitoring.
Modify specifications to reflect process changes and operational learnings.
Conclusion
The availability of heat exchanger process data sheet downloads plays a critical role in designing and operating efficient thermal systems. Properly prepared data sheets ensure that heat exchangers meet performance expectations, comply with industry standards, and operate cost-effectively.
However, balancing factors such as efficiency, cost, material selection, and regulatory requirements presents challenges that engineers must navigate carefully. By adopting best practices, leveraging accurate data, and utilizing advanced selection tools, industries can optimize their heat exchanger performance, ensuring long-term reliability and sustainability.
Whether for new installations or system upgrades, understanding the intricacies of heat exchanger process data sheets is essential for achieving operational excellence in heat transfer applications.
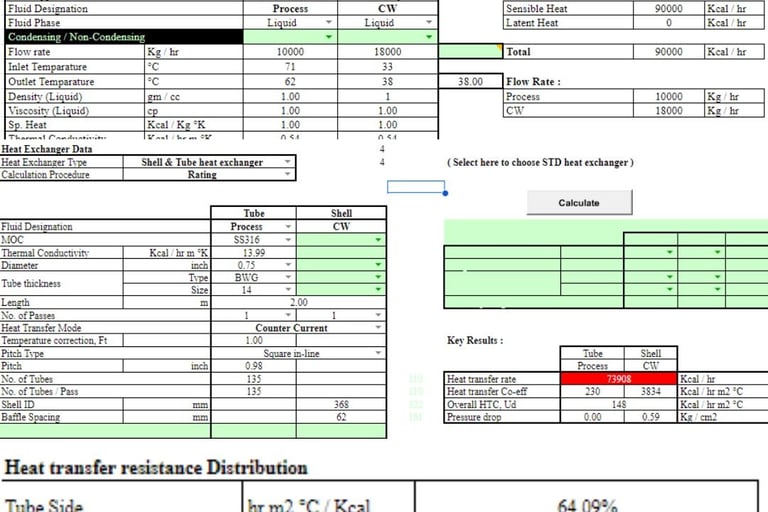
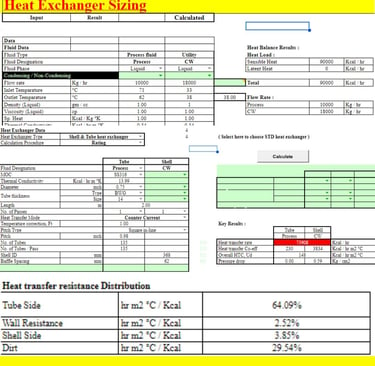
My post content